Have you ever wondered how residential and commercial roofs differ? Contrary to what you might think, the differences are not just in their size or the materials used. As a Chicagoland commercial roofing contractor, however, we can say with certainty that the matter is much more complicated. In the pages of this article, we will try to explain to you what the differences between residential and commercial roofing are and what they entail.
Table of Contents
Design and Structural Differences
At a glance, you can see that the roofs used in commercial construction differ from those installed on houses. Typically, office buildings, schools, warehouses and other similar structures have roofs with relatively low curvature. This, in turn, forces the use of other construction solutions. In the vast majority of cases, BUR, TPO, modified bitumen layers or metal roofing sheets are used.
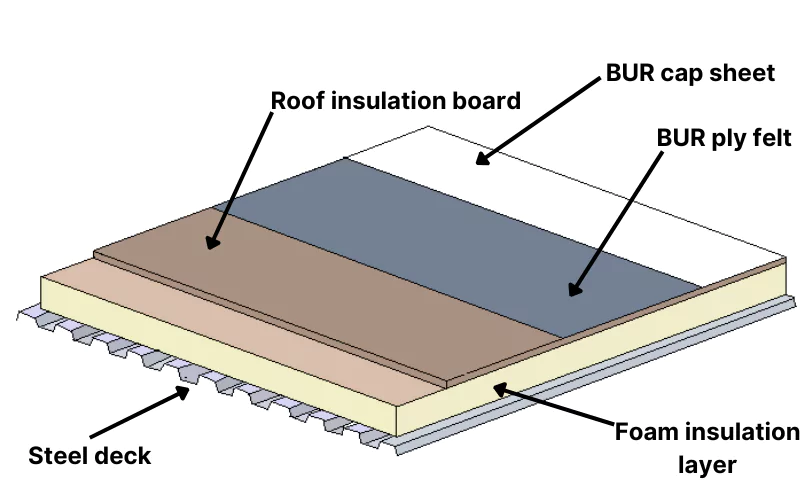
Due to user expectations, residential buildings need to be designed in such a way that their roofs do not need to be cleared of snow as often. Usually, there is also no need to maximize the used space – for this reason, walls in attics can be sloped and the height of the rooms lower. As a result, the construction of roofs on single-family houses usually consists of load-bearing elements that form a triangular shape in cross-section. Rafters and ridge board make up the framing that transfers loads to the building walls, while the outer layer is sheathing, which is covered with underlayment and rooftop material, such as asphalt shingles or cedar shakes.
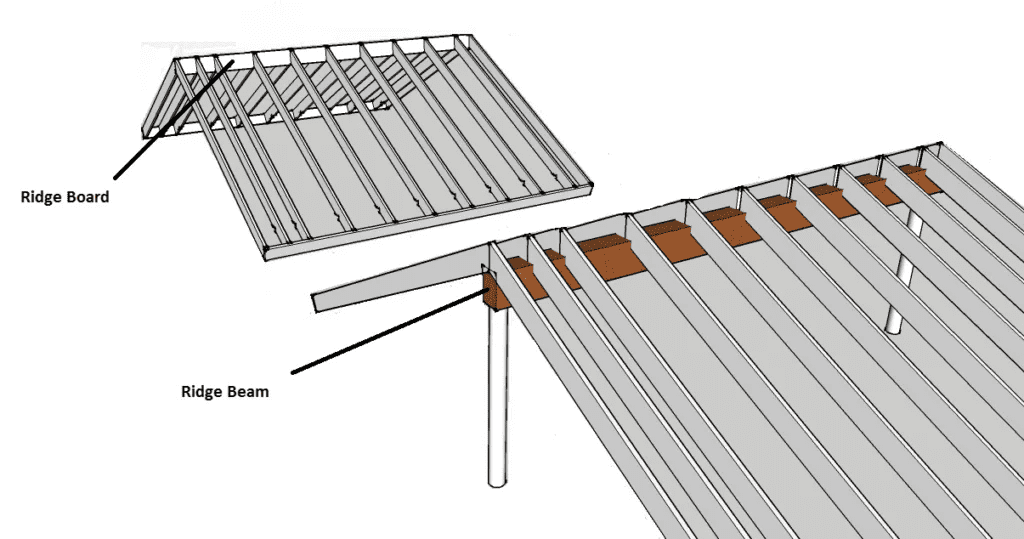
Let’s also point out that many roofs on residential buildings are designed to last much longer. Warehouses and office buildings are often built to last 20-30 years, while not long ago a detached house was expected to serve its owner for no less than 5 decades. This, in turn, translates into a different design philosophy – structural elements are thicker and stronger and can carry relatively much higher loads.
We should also add that commercial roofing systems are designed so that ventilation ducts, HVAC equipment, photovoltaic panels as well as many other elements can be installed on them. This makes it necessary for the roof plane to accommodate regular movement. Usually, the installation of many electrical conduits as well as fire protection systems is also envisioned at the design stage.
Materials Used
We have already mentioned that roofs on commercial buildings have a completely different structure from that encountered in residential construction. So it’s easy to guess that the differences also lie in the choice of materials.
Materials Used in Commercial Roofing
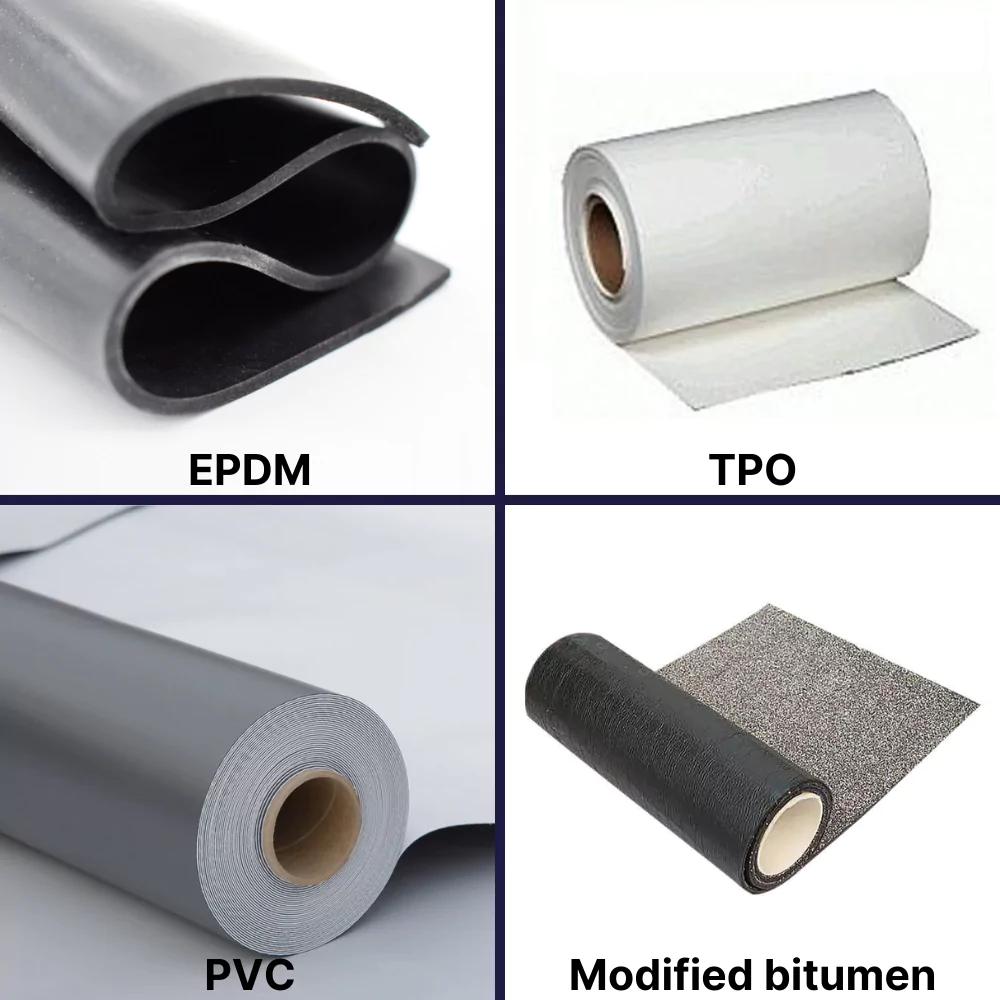
For commercial applications, the use of wooden structural elements would not be advantageous, mainly due to the price of manufacturing them and the limitation in the length or thickness of the beams. For this reason, steel, composites and even gravel are primarily used for roofs on warehouse halls, office buildings and factories. What matters most is low cost per square foot and high durability, while aesthetic considerations recede into the background.
Industrial and commercial roofing primarily use singly-ply membranes EPDM (ethylene propylene diene terpolymer), TPO (thermoplastic olefin), and PVC (polyvinyl chloride). In some cases, modified bitumen or BUR are also used.
Materials Used in Residential Roofing
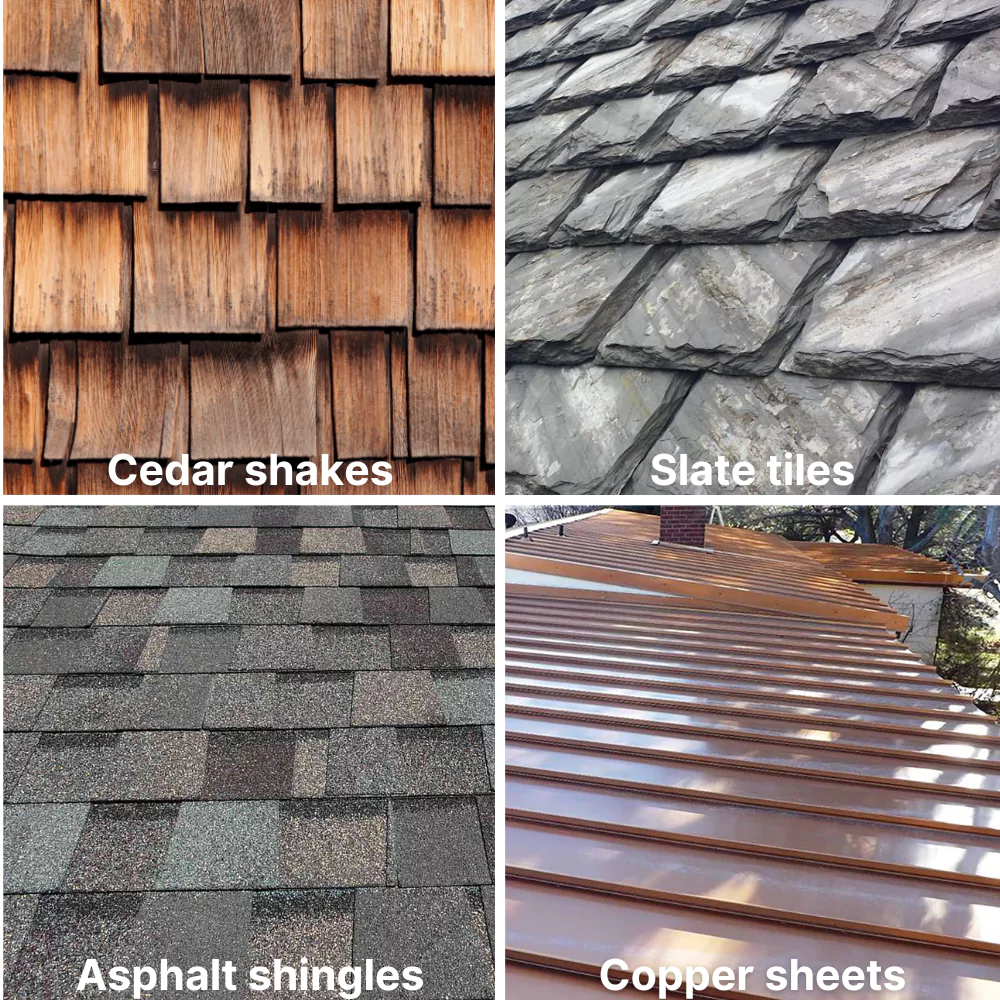
Roofs on houses don’t have to be that cheap, but their users expect much better aesthetics, even at the expense of durability. For this reason, customers are opting for asphalt shingles, slate tiles, cedar shakes and even copper sheet.
It is also worth knowing that the construction of roofs on residential buildings is wooden also because of its insulating properties. Unlike metal, wood protects the attic quite well from getting noises and escaping heat energy. This is important because temperatures in our homes tend to be higher than in offices or factories. While staying in residential buildings, we also expect much better acoustic conditions, so sound attenuation is an extremely desirable feature of roof construction.
Możesz się jednak domyślić, że zarówno drewniane belki nośne jak i asphalt shingles, które są najczęściej wykorzystywanymi materiałami dekarskimi w Stanach Zjednoczonych, są o wiele bardziej wymagające jeśli chodzi o konserwację. Jako regularnie zajmujemy się usuwaniem fragmentów dachów, które zajęte są przez pleśń. Zwykle, materiały używane w residential roofing już po około 15-20 latach wymagają szeroko zakrojonej konserwacji, a często nawet wymiany.
However, you can guess that both wooden support beams and asphalt shingles, which are the most commonly used roofing materials in the United States, are much more demanding when it comes to maintenance. As a roofing contractor operating in Chicago North Shore area, we regularly deal with the removal of roof sections that are occupied by mold. Typically, materials used in residential roofing already require extensive maintenance and often even replacement after about 15-20 years.
Installation Techniques
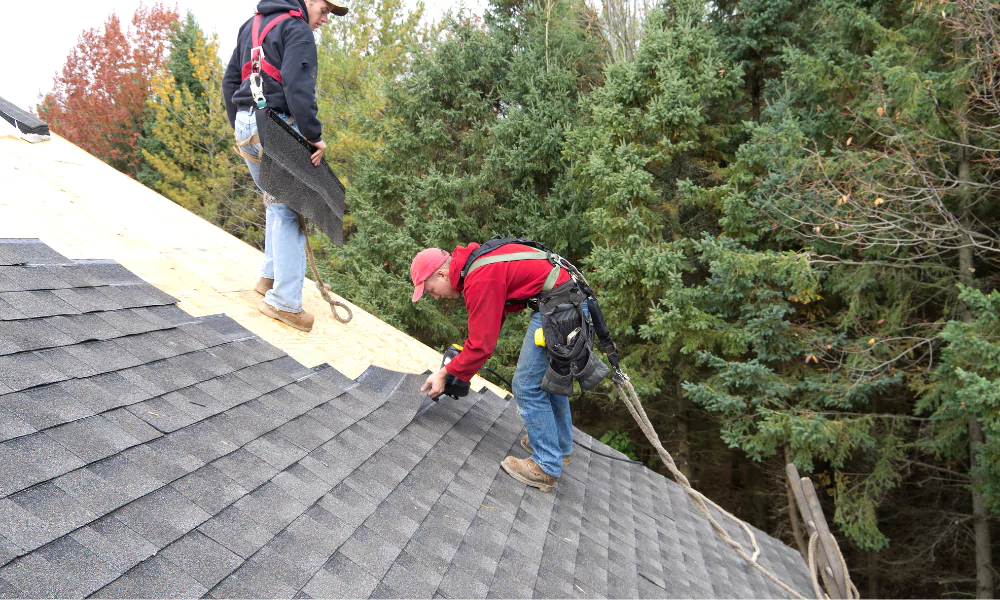
The process of installing roofs on residential buildings is also different from that of larger commercial and industrial buildings.In most cases, the amount of work devoted to each square (100 sqft) is greater.
Smaller tools are also used, which are tailored to the specific materials used.
In simple terms, the classic roof installed on a residential house consists of a wooden frame, on which boards or sheets of plywood are laid. These, in turn, are protected from the top by underlayment, while from the bottom by a layer of thermal insulation. At the very end, a rooftop is installed on the roof, a layer that protects the entire structure from the adverse effects of water, snow, UV radiation and other external factors.
Installing shingles, tiles and shakes requires the use of hundreds of nails, which are driven with hammers or specialized guns that press them into the wood with great force. This requires attention, as inadequate attachment of rooftop material can lead to leaks, which would inevitably lead to mold growth and degradation of the wood that makes up the roof structure.
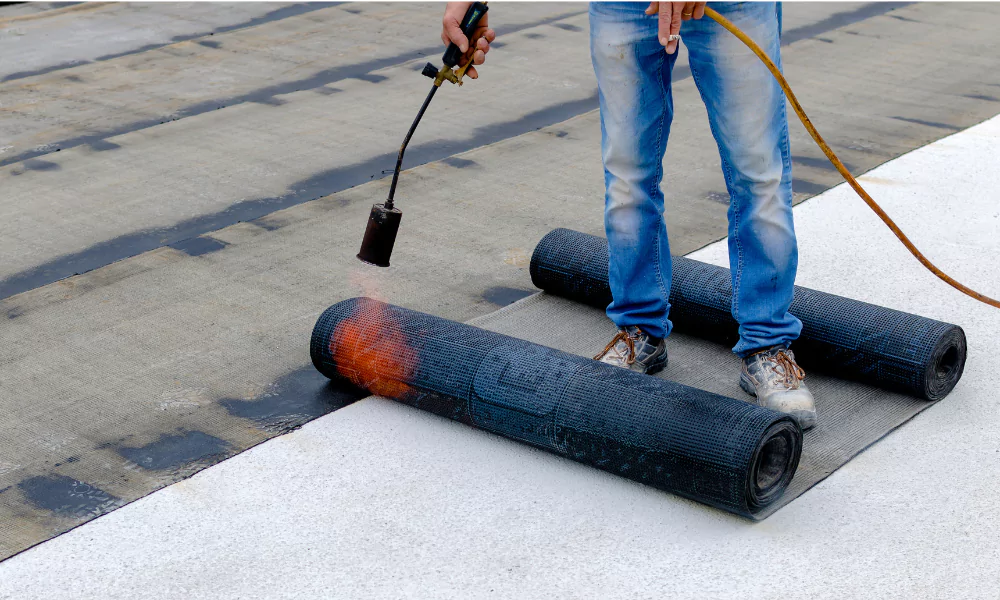
Roofs on large-scale buildings are usually installed on metal trusses. Depending on the chosen construction technology, sheathing is installed on the substructure to form the base for single-ply membranes or roofing panels are laid directly.
To ensure a high level of airtightness and to speed up installation as much as possible, single ply membranes and modified bitumen are glued or melted using gas burners. The whole process is much faster, but it is not always possible, because the bonding of some polymers does not work properly in high humidity or in freezing weather. Let’s also point out that flat roofs need to be much better protected against water penetration – it’s natural that puddles form on their surface, and even the slightest damage to the entire structure would instantly result in leaks.
Maintenance and Repair
The differences between residential and industrial roofing are also apparent on the maintenance front. Roofs on factories, warehouses and public buildings are regularly inspected as a result of current regulations and internal bylaws. In many cases, regular snow removal and even washing of the entire surface is also necessary to reduce heat build-up. However, if a single-ply membrane becomes damaged, a very large section of it may need to be replaced.
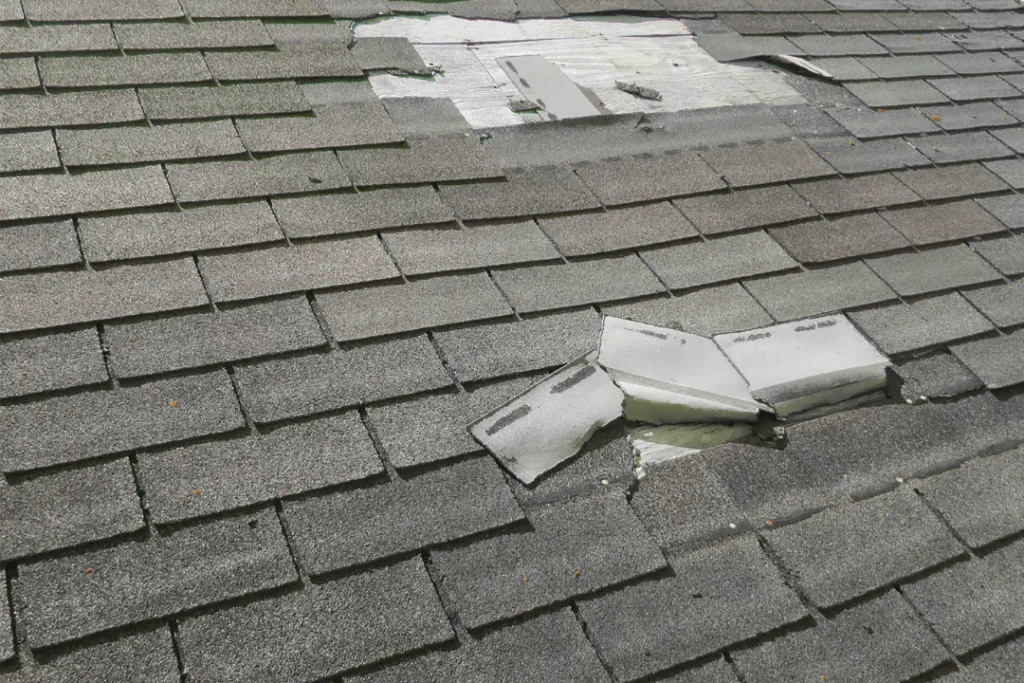
The specifics of the maintenance of roofs located on houses depends, of course, on the material used and the attitude of the owner himself. Nevertheless, it can be assumed that the vast majority of roofs on houses are inspected and cleaned less frequently. In some cases, however, the repair is simpler – a huge advantage of shakes and tiles is the ability to replace individual components of the entire structure, which reduces costs.
Differences in Terms of Initial Cost
Money is a very important factor, whether we are talking about commercial roofing or residential construction. Keep in mind, however, that the area of warehouses and factories can sometimes be hundreds of times larger, so even minimal differences in the price of sqft roof installation can translate into thousands, not tens of dollars.
Due to higher requirements for fire safety, waterproofing and longevity, the cost of installing a large-surface roof on an industrial or commercial building is up to three times higher compared to residential homes. Installing a single-ply membrane along with the labor costs of a roofing contractor costs from $11 to $15 per sqft, while asphalt shingles, popular in residential construction, along with installation services, will purchase for as little as about $5 per sqft.
Typically, commercial roofing uses more complicated technologies, and the slopes themselves must be adapted to carry much higher loads, for example, due to the presence of lingering, melting snow.
Functionality and Purpose
Industrial and commercial roofing is also governed by other functional requirements. Typically, in addition to its insulating and protective function, roofs on warehouses and office buildings are spaces where various equipment necessary for the proper functioning of the building is installed. Ventilation ducts, air-conditioning equipment, solar panels, fire protection systems and even recreational spaces are not located in the interior, allowing most of the volume of the entire building to be used for business purposes.
In the vast majority of cases, the only use of roofs installed on houses is to protect the interior from rain and cold. Unlike commercial roofing, residential roofs are relatively simple structures with a very straightforward design, with the only complications being possible skylights, chimneys and ventilation elements.
Energy Efficiency
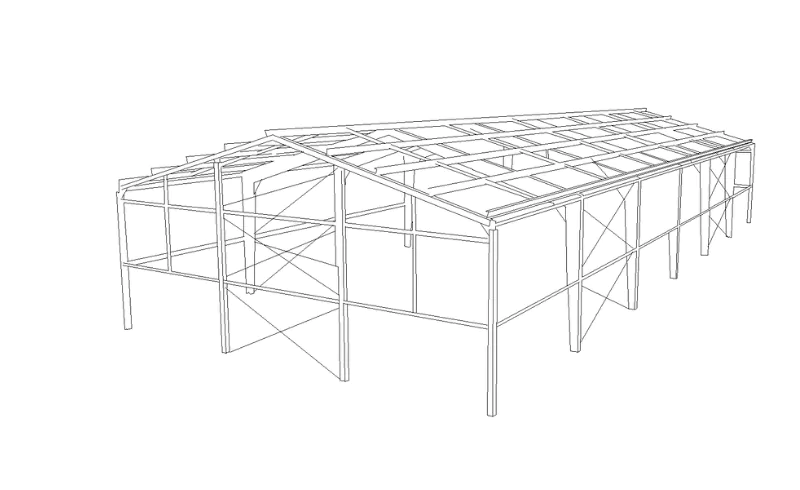
Ensuring high energy efficiency in commercial roofing is a much more difficult task. Because of the significant room heights in many industrial buildings, the rate of thermal energy escape through large-scale roofs is much higher – there is a stack effect.
Achieving the same, or even better, insulation performance on house roofs is not as crucial, since the ratio of roof to floor area is simply smaller, so interior heating and cooling costs are lower. In addition, attic volume can be significantly reduced as a result of a thicker insulator layer, which would not be desirable for many industrial buildings. Finally, it should be added that commercial roofing systems usually come with a lot of additional installations, and for each of them additional openings are needed in the roof, which of course worsens the insulation performance of the entire structure.